How To Choose Screen For High-quality Printing?
- Share
- Issue Time
- Nov 27,2024
Summary
In recent years, the requirements for screen printing technology have been rising year by year, so that various fields have begun to mass-produce filaments below 50 microns for printing. As we all know, screen printing is widely used. In order to achieve high-quality printing, everything from material selection to printing condition setting must meet the requirements.
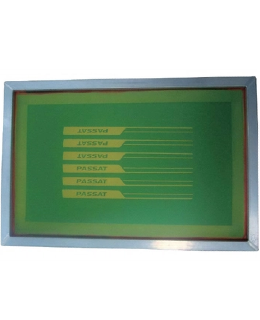
In recent years, the requirements for screen printing technology have been rising year by year, so that various fields have begun to mass-produce filaments below 50 microns for printing. As we all know, screen printing is widely used. In order to achieve high-quality printing, everything from material selection to printing condition setting must meet the requirements.
1. Strength
The use of screens is based on mass production, so try to choose screens with high strength. The strength of the screen has a great impact on the release, clarity and accuracy of printing, and the service life of the screen, so the strength of the screen is the most important reference value when choosing. Because the finer the screen, the weaker the strength, so special attention should be paid when printing precision wiring. If there are high requirements for printing accuracy, or if the use of high-viscosity dyes makes it difficult to release the screen, it is recommended to use a high-strength screen (high-strength stainless steel screen).
2. Opening rate
The size of the opening rate affects the amount of ink during printing. Too high an opening rate will result in excessive ink, making the image unclear. Asada Precision Mesh recommends using a screen with an opening rate of 40% for precision wiring printing.
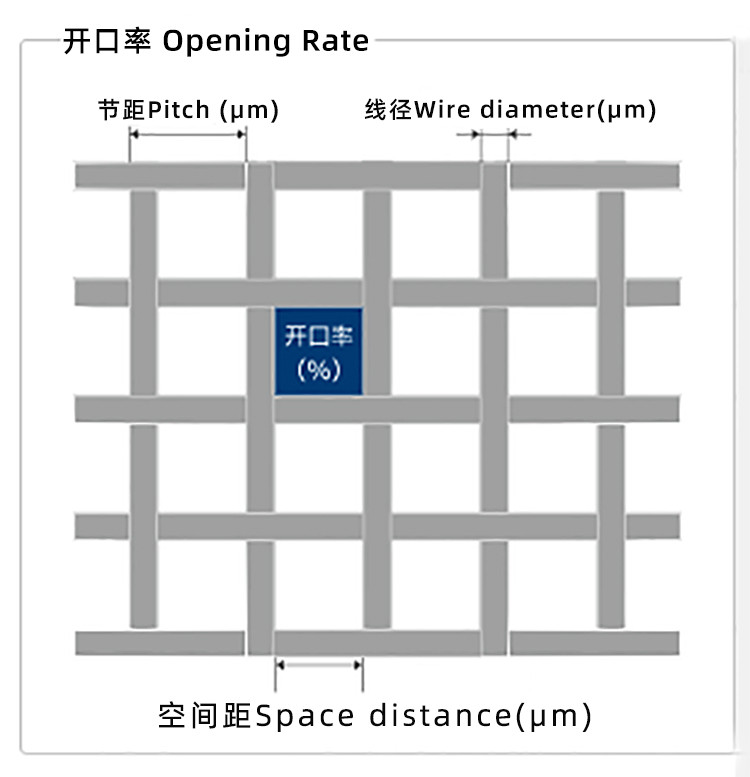
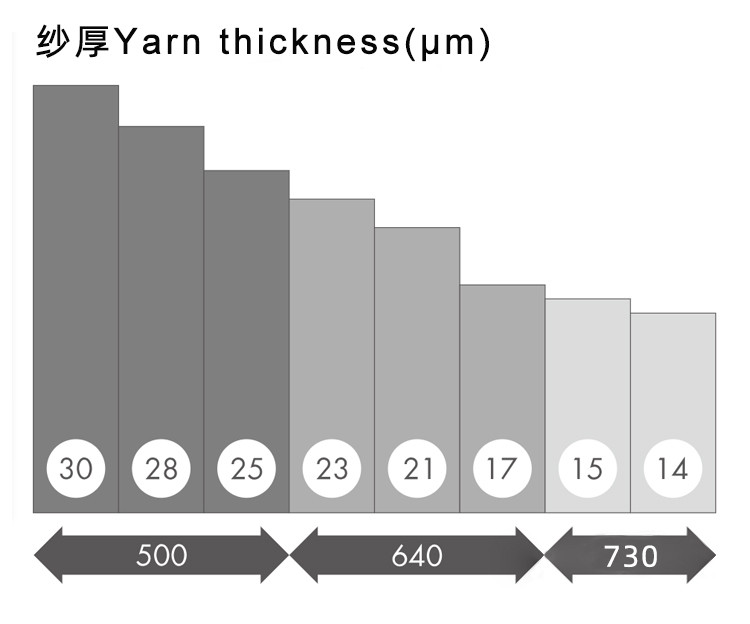
3. Yarn thickness
When the opening size of the screen is more than twice the screen pitch (25.4mm÷mesh number), the printing state is the most stable. When the ink performance is high, it can also show good printing effects at a pitch of 1.5 times. If the viscosity and elasticity of the ink are at their best, printing can be done as long as it is greater than 0.8 times the pitch.
The MLCC market has high requirements for thin layers and uniformity, and now uses 500-mesh, 640-mesh and 730-mesh thin-rolled products. Processing thickness can be adjusted in 1-micron increments, allowing rolling to sub-micron tolerances based on the desired printed film thickness.
4. Number of meshes
When the plate opening width is more than 2 times the stainless steel precision mesh pitch (25.4mm÷mesh number), the printing state is the most stable. If the ink quality is high, high-quality images can be printed at 1.5 times the pitch. If the viscoelasticity of the ink is adjusted to the optimal state, it can be printed at 0.8 times the pitch.
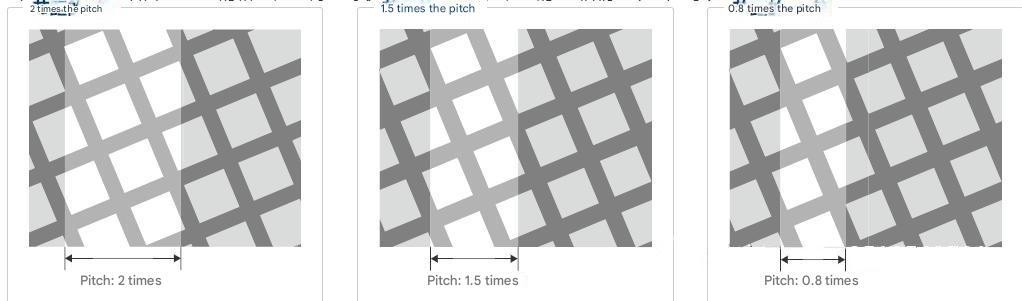
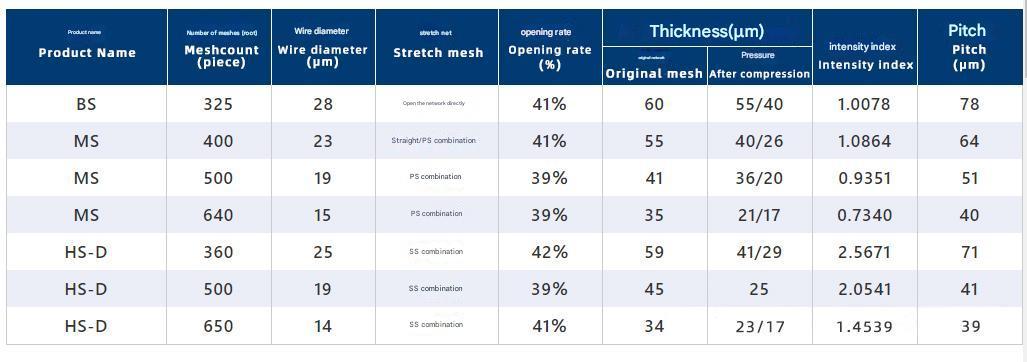
5. Silk screen (A standard)
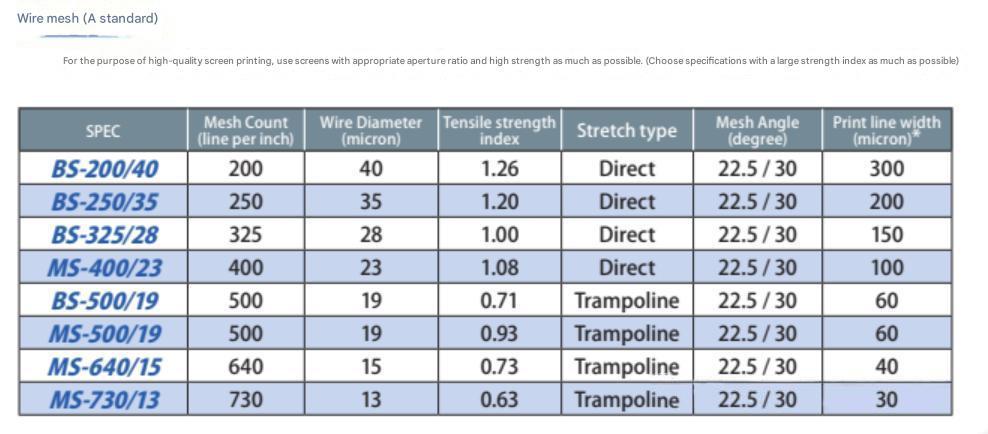
6. Strength index and recommended tension of wire mesh
The strength of the wire mesh will vary depending on the material strength, wire diameter, and mesh number. AsadaMesh uses BS325 mesh (wire diameter 28 um) wire mesh as the benchmark, calculates the relative [strength index] of various specifications and recommends tension based on the [strength index].
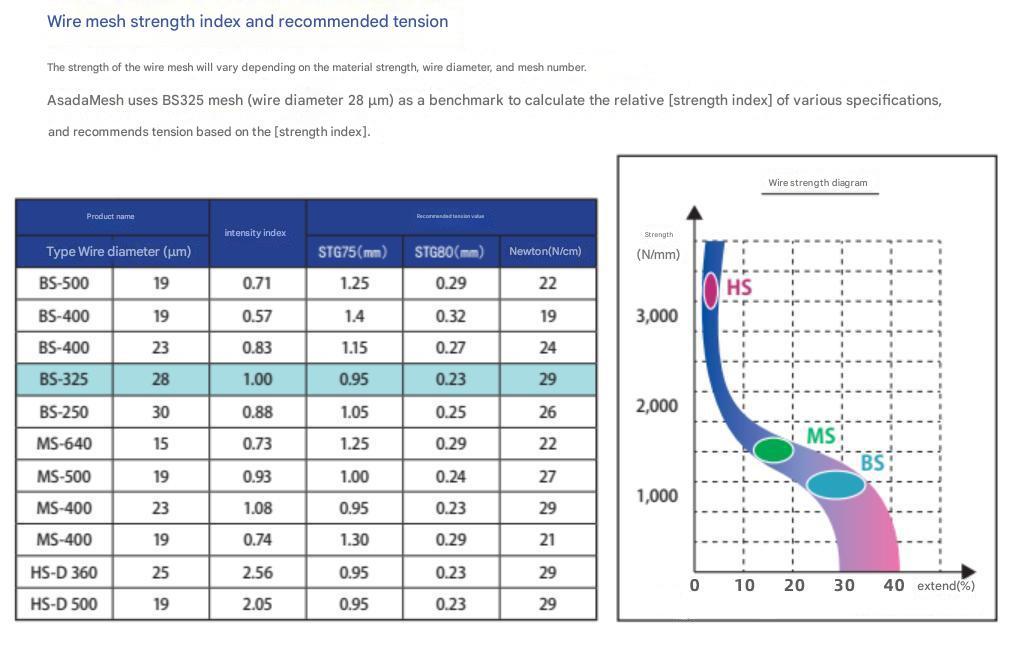
7. Ultra-high strength HS-D wire mesh
The ultra-high-strength HS-D screen uses a 150-mesh metal mesh SS composite structure mesh as the outer yarn, which can be made into a "non-deformation screen". Even if the distance from the plate is twice the standard, there will be no "plate deformation". It can be used for printing high-viscosity slurries and printing with high requirements for printing dimensional accuracy. It has the characteristics of long screen life.
