How to choose the correct printing screen frame size?
- Share
- Issue Time
- Aug 21,2024
Summary
The advantages of aluminum screen printing frame are its durability and service life. Unlike the wooden screen printing frame, the aluminum frame immersed in or exposed to water in the sink will not deform.
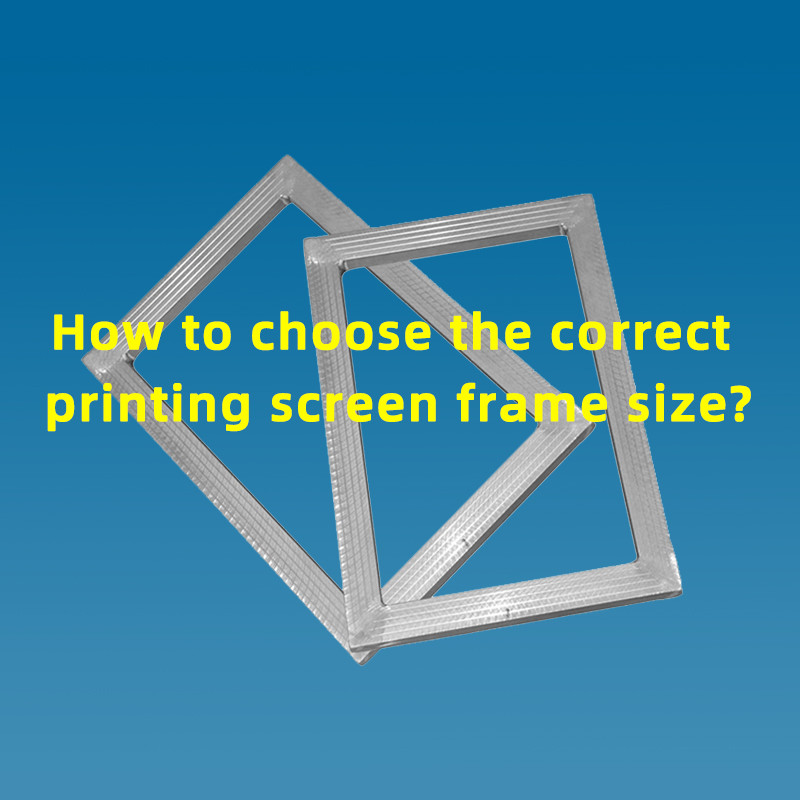
Information about frame types
The advantages of aluminum screen printing frame are its durability and service life. Unlike the wooden screen printing frame, the aluminum frame immersed in or exposed to water in the sink will not deform. This will ensure a flat frame in thousands of prints in the future. The aluminum frame can also be stretched and re-stretched several times. Only use professional tools that will not damage the aluminum to remove the mesh and glue from the frame. Once cleaned, the frame can be stretched again, which will give you the opportunity to use the frame in years of hard work in the workshop. The aluminum frame is also very light, which reduces the transportation cost and can save money in the long run. If you want to optimize the performance of the store, the aluminum frame is a good element added to the screen printing equipment.
More information about screen print grid size:
Different mesh sizes are used for different applications in the screen printing process. The grid size is measured by the number of grid lines crossed per square inch. For example, the 110 mesh screen has 110 cross yarns per square inch. The higher the number of meshes, the thinner the lines and holes on the screen. The mesh size largely depends on the accuracy of the image and the thickness of the ink used. If your image has very high detail, the lower grid screen will not consider high detail. Thin lines or points in the image will only pass through the mesh holes, which will not give you a correct representation of what the image should be. In addition, if thinner ink is used, the ink will also enter larger holes and penetrate into the shirt or substrate, and the image will become blurred with ink bleeding. On the other hand, if you try to print thicker ink (such as white) to a high grid screen, almost no ink will print through the grid. You will notice that different companies have different sizes. If the number of meshes is very close, such as the difference between 155 and 156, 196 and 200, or 81 and 86, the difference is very small and will not affect the final result. Because screen printing involves many variables, we cannot tell you exactly which grid sizes are used for which applications. However, we can provide you with a general overview of the formats used for certain types of printing.
The basic size and the most common grid size are 110 and 156. The grid 110 establishes a fairly thick ink layer. It is very suitable for large printing fonts and matching color patterns. It is also the recommended grid for white flash boards, because you usually only need to print once, which speeds up the production time. The mesh 156 also creates a slightly thicker layer of screen printing ink, but because the mesh is thinner, the image details are more accurate. Similarly, if printing with a slightly thinner ink color, grid 156 can be used to avoid too much ink passing through the screen. A lower mesh number, such as 40 to 86, is used for shiny and glossy inks. These inks contain particles that do not cross typical grid sizes. Therefore, you need a lower number of meshes with large holes so that all particles can pass through correctly. Plastisol Shimmer ink contains finer particles, so you may use an 86-mesh screen, while flash ink contains larger particles. Therefore, 40 or 60 mesh sieve is recommended. 200 and 230 meshes are used for more detailed images and finer inks. These grid sizes may contain large halftone points, but are not recommended for four-color printing or halftone printing with precise details. Thinner graphics and solvent-based screen printing inks are also applied to these grids. In addition, if you want the ink on the shirt to be softer, you can use these higher grid numbers to print, which will leave less ink on the screen, which will make you feel softer on the shirt. This may be difficult, but it usually needs to get a darker appearance in trouble, but if you want to get bright and bright colors (especially white), it will be difficult to get enough thick opacity with these higher meshes. The grid 305 is used for very high detail textile printing, as well as fine four-color printing and analog printing. (To learn more about process printing, click here.) Fine halftone points require a fine detail grid to save and display. The upper grids such as 355, 380 and 400 are mainly used for graphic printing with UV ink. UV ink is very thin and is usually used to print high details on panels, banners or CDs. Using a higher grid allows the automatic printer used in UV printing to adjust the amount of ink passing through the screen.
Exhibition description:
Due to the size of the holes in the grid, different grid sizes contain different amounts of lotion. For example, the 110 mesh sieve contains more lotion than the 305 mesh sieve. Although the difference is not extreme, you need to change the exposure time slightly for different mesh sizes. A thinner sieve that retains less lotion will be exposed more quickly than a lower sieve that contains more lotion. However, the difference is very small. You may only need to slightly change 5% to 10% in both directions, depending on the mesh size, to achieve maximum exposure performance.