Introduction to screen printing of conductive silver paste layer on PVC film of smart atomized glass
- Share
- Issue Time
- Dec 9,2024
Summary
Smart atomized glass is a high-tech material that controls the transparent and atomized states through voltage. One of its core components is the conductive silver paste layer. Using screen printing technology to accurately print the conductive silver paste onto the PVC film is a key part of the manufacturing process. The following is an introduction from the aspects of process difficulties, equipment selection, operation procedures and precautions.
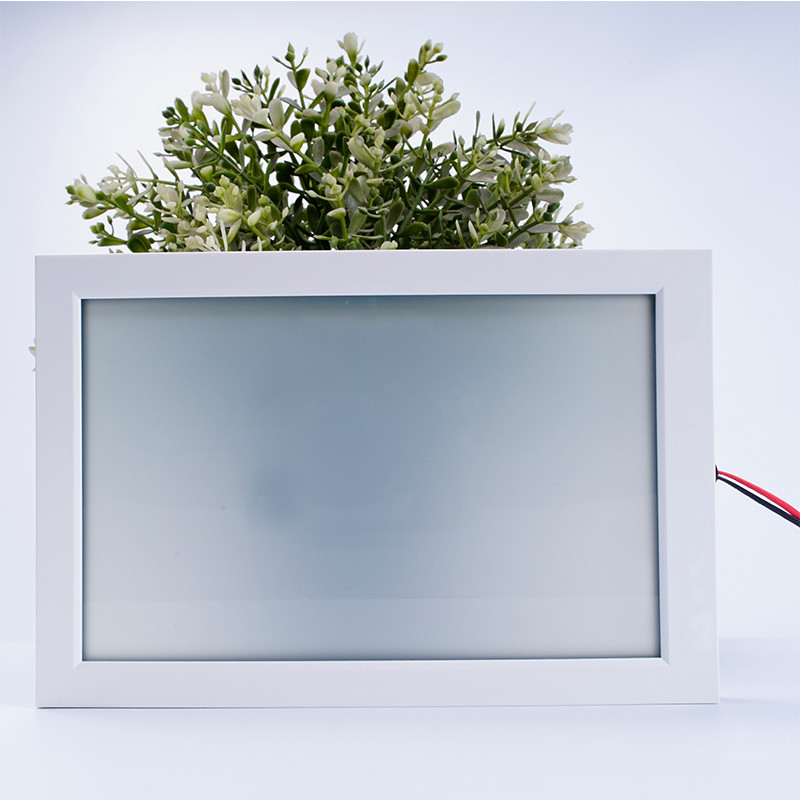
Smart atomized glass is a high-tech material that controls the transparent and atomized states through voltage. One of its core components is the conductive silver paste layer. Using screen printing technology to accurately print the conductive silver paste onto the PVC film is a key part of the manufacturing process. The following is an introduction from the aspects of process difficulties, equipment selection, operation procedures and precautions.
I. Process Difficulties
1.Uniformity and conductivity : The distribution of conductive silver paste directly affects the uniform conductivity and optical properties of the circuit. It is necessary to ensure consistent thickness to avoid open circuits or short circuits.
2.Adhesion and compatibility : Silver paste needs to be highly compatible with the PVC substrate, have strong adhesion after printing and cannot fall off due to processing or long-term use.
3.Pattern precision : Circuit designs are usually fine grids, requiring high-precision screen templates and printing technology.
4.Temperature control and drying : After printing, the silver paste needs to solidify quickly. The control of temperature and time directly affects the conductive properties and adhesion effect.
II. Printing equipment used
1.Screen printing machine : Use high-precision automated flat screen printing machine to ensure stable printing quality.
2.Silk screen template : Use high mesh (300~400 mesh) stainless steel silk screen or polyester silk screen, with precise pattern engraving and uniform mesh.
3.Scraper and coating system : Equipped with a polyurethane scraper with adjustable pressure to ensure uniform distribution of the slurry.
4.Drying equipment : infrared dryer or hot air dryer, used to quickly solidify the silver paste layer.
III. Operation process
1.Screen preparation : Clean the screen template to ensure it is free of dust, grease and other impurities.
2.Paste preparation : adjust the viscosity according to the recommendations of the silver paste manufacturer and add appropriate amount of diluent if necessary to ensure printing fluidity.
3.Positioning and fixing : Fix the PVC film on the printing table, align the screen and film pattern to avoid deviation.
4.Printing operation : Apply even pressure to the scraper and move it smoothly from one end to the other to ensure that the slurry fills the mesh evenly.
5.Initial inspection : Use a magnifying glass to check the print to make sure there are no missing prints or bubbles.
6.Drying and curing : The printed PVC film is sent into the drying equipment and cured at the specified temperature and time.
7.Testing and quality inspection : Conductivity, adhesion and optical performance tests ensure compliance with requirements.
IV. Precautions
1.Strictly control the temperature and humidity of the printing environment to avoid the slurry from curing too quickly or lacking fluidity.
2.Stir the slurry thoroughly before printing to avoid precipitation of silver paste particles.
3.When cleaning the screen, you need to use a special cleaning fluid to avoid mesh clogging and affecting printing quality.
4.During operation, avoid excessive or insufficient scraper pressure to prevent damage to the screen or insufficient silver paste.
5.Regularly maintain equipment to ensure printing accuracy and consistency.
Through scientific process control and meticulous operation, the intelligent electrically-controlled atomized glass interlayer PVC conductive silver paste screen printing process can achieve mass production of high-quality products and provide strong support for the industry's technological development.