The Innovative Journey of Multi-Color Printing on Glass Glue Bottles with Screen Printing Technology
- Share
- publisher
- Taoxing technology
- Issue Time
- Sep 21,2024
Summary
In today's article, we will dive into the world of multi-color printing on glass adhesive bottles and explore how servo-cylindrical screen printers shine in this field!
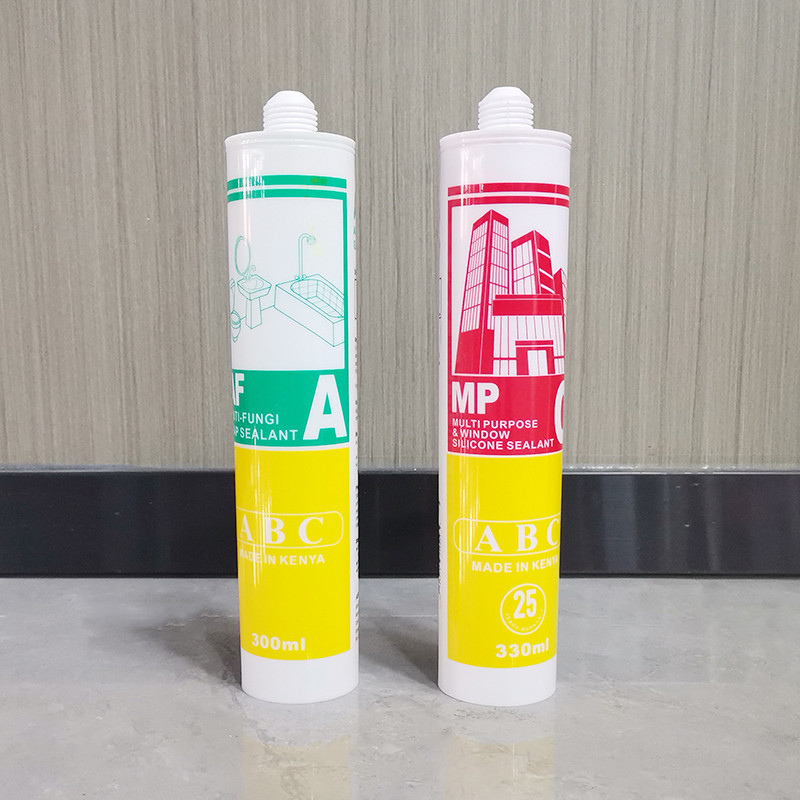
Hello everyone, we will dive into the world of multi-color printing on glass adhesive bottles and explore how servo-cylindrical screen printers shine in this field!
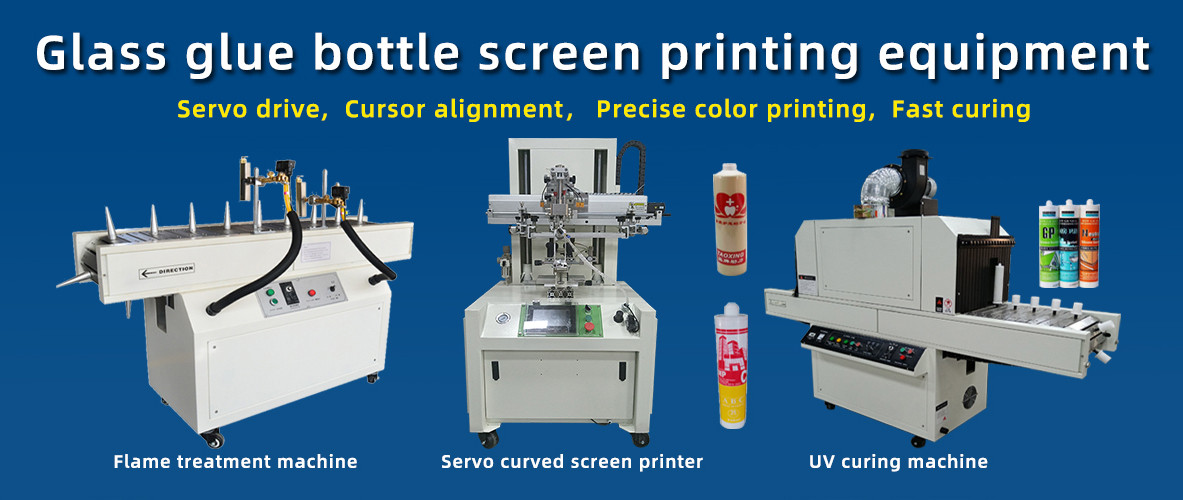
The Challenges of Printing on Glass Glue Bottles
Let's first focus on the unique challenges of printing on glass glue bottles. Glass glue bottle is both hard and transparent, which means that the ink not only needs to adhere firmly but also maintain pure colors when light passes through. Moreover, the curved design of the bottles adds complexity to the printing process, making it difficult for traditional printing techniques to achieve the desired effects, often resulting in blurry patterns and uneven colors.
The Advantages of Screen Printing Technology
So, what technology can break through these challenges? Screen printing technology stands out due to its unique advantages. Screen printing is a technique where ink is transferred onto a substrate through a patterned mesh screen. It offers thick ink layers, strong resistance to light and weather, and wide adaptability, making it particularly suitable for glass materials.
*Thick ink layers: Ensuring high color saturation and clear edges of the patterns.
*Strong resistance to light and weather: Good adhesion of the ink, preventing color fading.
*Wide adaptability: Capable of handling both flat and curved surfaces with ease.
The Performance Characteristics of Servo-Curved Screen Printers
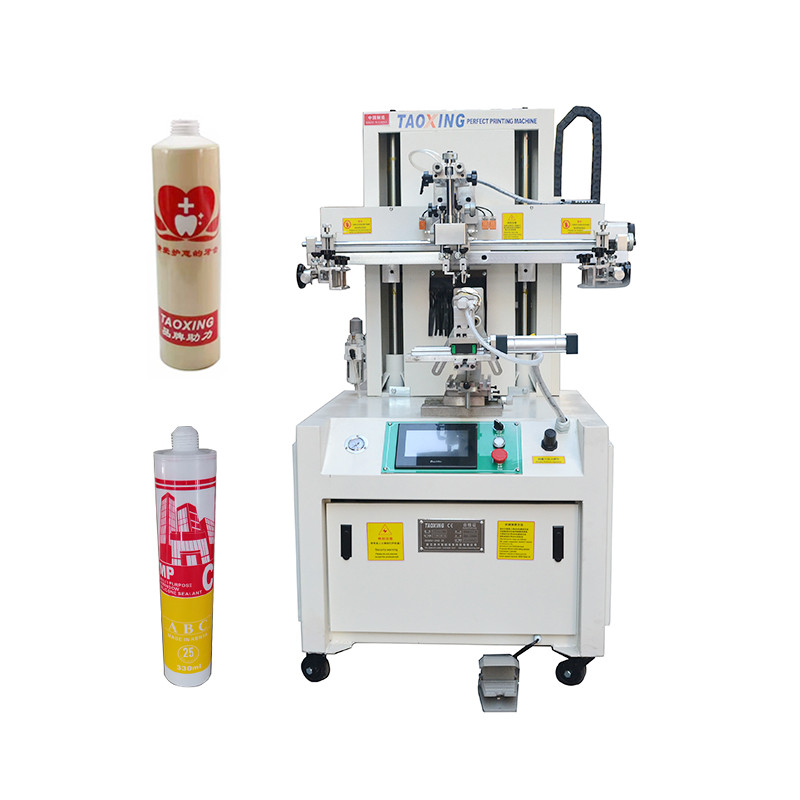
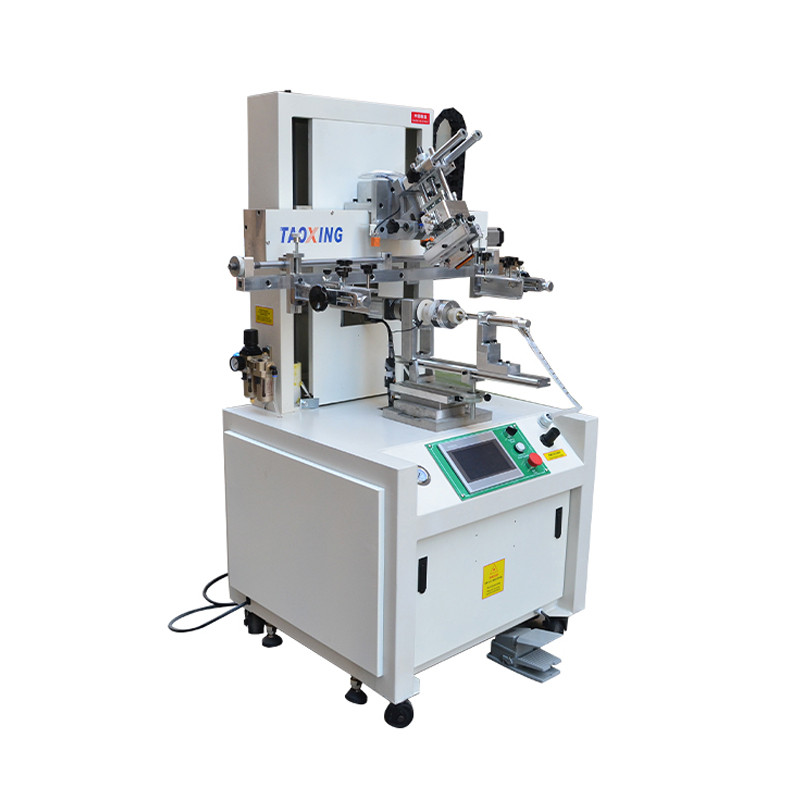
When screen printing meets the servo-curved screen printer, the perfect solution is born. With its advanced servo motor control system and precise mechanical structure, the servo-cylindrical screen printer achieves high-precision control over curved surface printing.
*High-precision positioning: Servo motors precisely control to ensure that patterns perfectly match the curved surface of the bottle.
*High level of automation: Reduces manual operations, enhancing production efficiency and consistency.
*Intelligent adjustment: Automatically adjusts printing parameters according to different materials and patterns.
Printing Operation Process and Precautions
So, is the operation process of such a sophisticated machine complicated? Actually, no, the operation process of the servo-cylindrical screen printer is straightforward, but here are some key points to keep in mind:
1.Preparation work: Clean the surface of the bottle to ensure it is dust and oil-free.
2.Calibrate the equipment: Perform fine calibration on the servo-cylindrical screen printer to ensure accurate patterns.
3.Color matching and trial printing: Mix colors according to need and conduct trial printing, making minor adjustments until perfect.
4.Monitor the printing process: Real-time monitoring of print quality, adjust promptly to avoid batch issues.
5.Post-processing: After printing, conduct appropriate drying and curing treatments for the printed items.
Conclusion
In summary, multi-color printing on glass adhesive bottles was a challenge with traditional printing technologies, but with the help of the servo-cylindrical screen printer, these problems are easily solved. The inherent advantages of the screen printing process, coupled with the advanced technology of servo-cylindrical screen printers, make the multi-color printing of glass adhesive bottles simple, efficient, and beautiful. From precise positioning to automated operations, from color mixing to quality monitoring, every step reflects the pursuit of perfect printing.
I hope this article has helped you to understand the charm of multi-color printing technology on glass adhesive bottles. If you are interested in servo-cylindrical screen printers or have any questions, feel free to leave a comment and let's discuss.