The factors that determine the amount of ink applied in screen printing
- Share
- publisher
- Taoxing technology
- Issue Time
- Oct 30,2024
Summary
In the screen printing process, the control of the amount of ink applied is a crucial link. It directly affects the final effect and quality of the printed product. So, in the screen printing process, what factors determine the amount of ink applied? Let's explore it together.
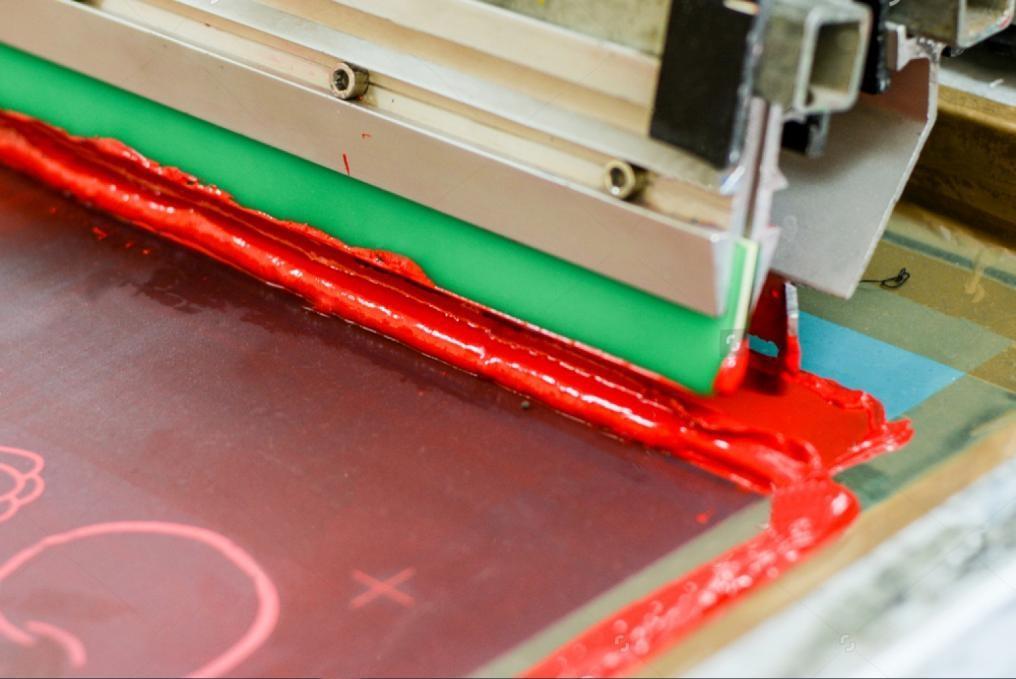
In the screen printing process, the control of the amount of ink applied is a crucial link. It directly affects the final effect and quality of the printed product. So, in the screen printing process, what factors determine the amount of ink applied? Let's explore it together.
1. Selection of Silk Screen
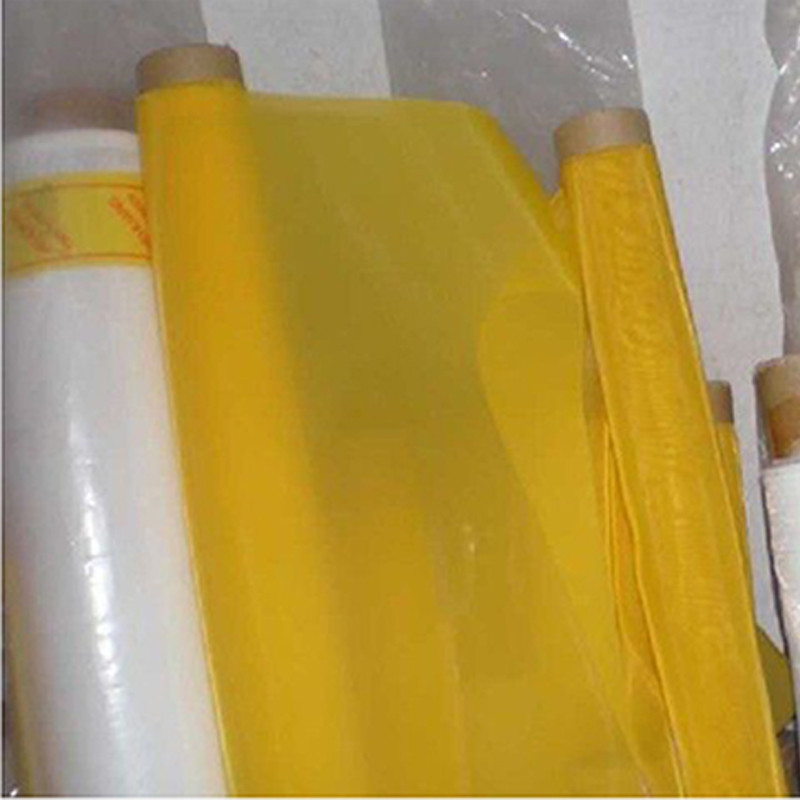
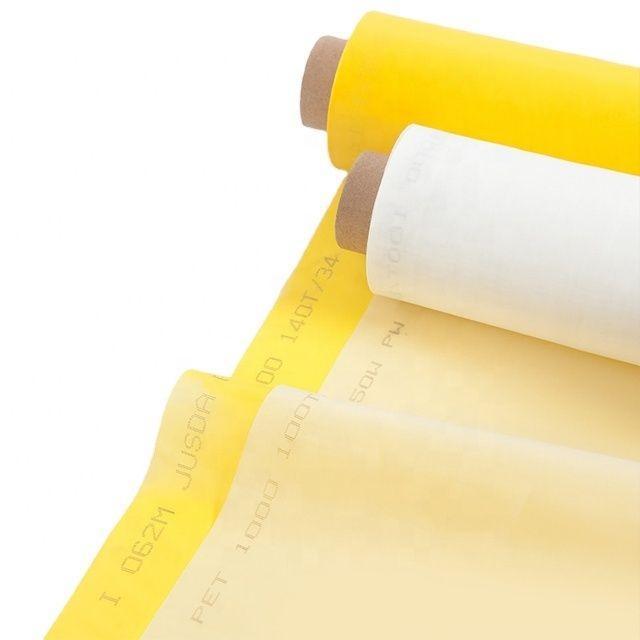
Mesh count: The mesh count of a screen refers to the number of holes per inch. The lower the mesh count, the larger the holes, and the more ink is applied; the higher the mesh count, the smaller the holes, and the less ink is applied. Therefore, choosing the right mesh count is crucial to controlling the amount of ink applied.
Wire thickness: Under the same mesh count, the thickness of the screen will also affect the amount of ink applied. The thicker the wire thickness, the more ink applied; the thinner the wire thickness, the less ink applied.
Mesh Type: Twill weave screens hold more ink than plain weave screens. This is because twill weave screens allow ink to pass through more easily during the printing process.
Tension: The tension of the screen will also affect the amount of ink applied. The greater the tension, the better the stability of the screen during printing, and the amount of ink applied will increase accordingly.
2. Characteristics of ink
Ink absorption: The ink's consistency directly affects the amount of ink absorbed. The thinner the ink, the more ink it absorbs; the thicker the ink, the less ink it absorbs.
Viscosity: The viscosity of the ink will also affect the thickness of the ink layer. The lower the viscosity, the thicker the ink layer; the higher the viscosity, the thinner the ink layer.

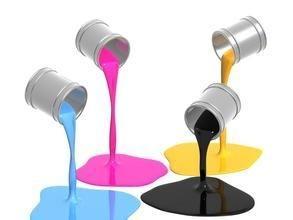
3. Film thickness of photosensitive paste
The thickness of the photosensitive paste during plate making also has an important influence on the amount of ink applied. The thicker the photosensitive paste, the more ink applied. This method is very commonly used in the process of increasing the thickness of the ink.
4. Scraping process
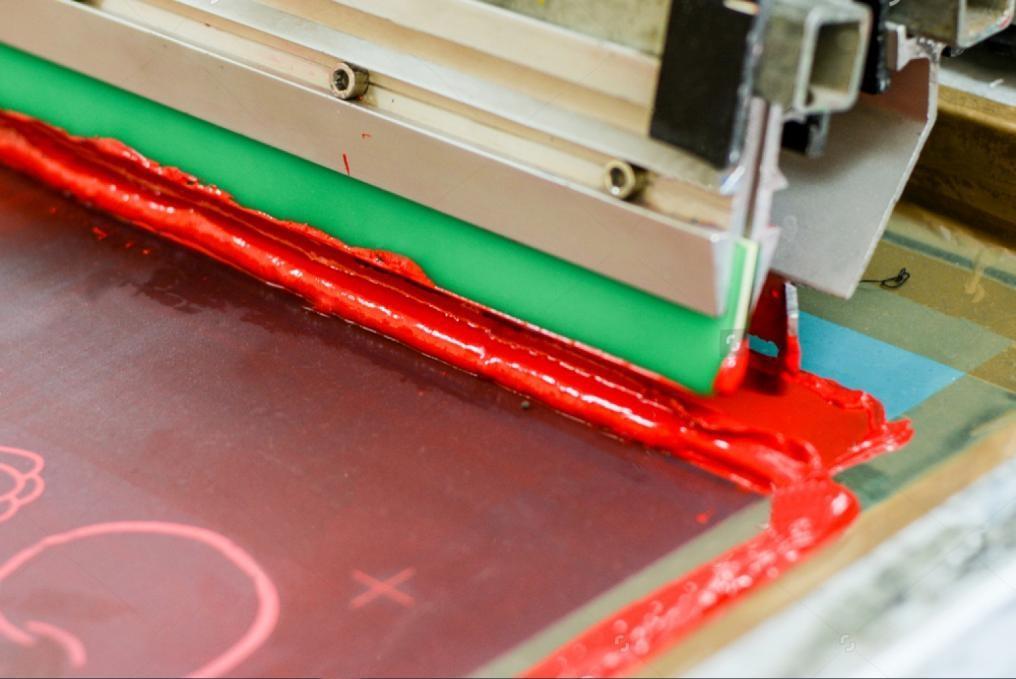
Scraping speed: The speed of scraping directly affects the thickness of the ink layer. Slow scraping speed means thicker ink layer and more ink; fast scraping speed means thinner ink layer and less ink.
Scraper: The material, slope, hardness and blade shape of the scraper will affect the amount of ink deposited. The softer the scraper, the greater the slope, and the more rounded the blade, the more ink will be deposited; conversely, the less ink will be deposited.
Scraper pressure: During printing, the pressure applied to the scraper will also affect the amount of ink applied. The greater the pressure, the ink will be driven away before it is completely squeezed out of the mesh, and the amount of ink applied will decrease; the smaller the pressure, the more ink applied.
5. Other factors
Screen tension: Screen tension not only affects the size of the opening, but also the mesh count, wire diameter and screen thickness, thus affecting the amount of ink applied.
Printing environment: Changes in temperature and humidity in the printing workshop will also affect the ink itself, thereby affecting the thickness of the ink layer and the amount of ink applied.
Printing materials: The ink absorption performance of the printing material will also affect the amount of ink applied. The material with good ink absorption performance will increase the amount of ink applied accordingly.
Through the above analysis, we can see that in the process of screen printing, the control of ink volume is affected by many factors. In order to obtain the ideal printing effect, we need to comprehensively consider these factors and make reasonable adjustments and controls. Only in this way can we ensure the stable quality and excellent effect of the printed products.